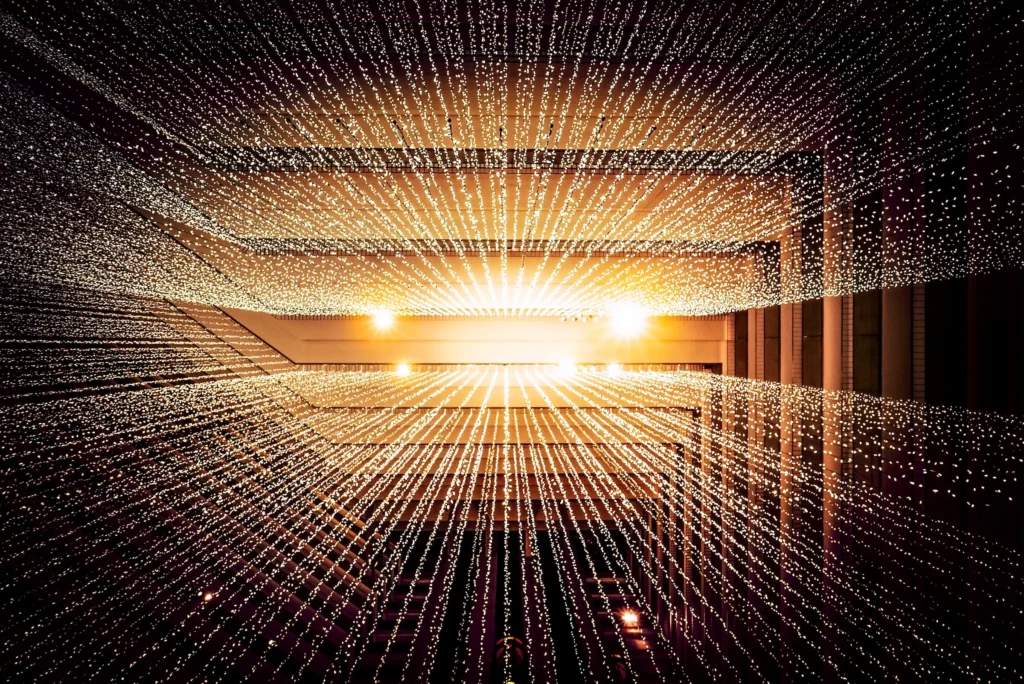
Maximizing Innovation and Efficiency: The Vital Role of Standardization in New Product Development
In the ever-evolving landscape of manufacturing, staying ahead of the curve is vital for not just surviving, but thriving. We understand the pivotal role that standardization plays in ensuring excellence in operations. In this blog post, we explore the significance of standardization in new product development and engineering practices. Read on to discover how embracing standardization can propel your business forward, featuring insights from industry experts, case studies, and research findings.
Structured Processes: The Backbone of Efficiency
Efficiency is the cornerstone of any successful manufacturing enterprise. Standardization introduces rigor and consistency, significantly reducing inefficiencies and the margin for error. With clearly defined workflows and procedures, precision is guaranteed at every stage of the product development cycle.
Industry expert John Smith, in his seminal work ‘Lean Manufacturing Principles,’ notes, “Standardization is the cornerstone of lean manufacturing. It offers a clear roadmap for companies to identify and eliminate wasteful practices, ultimately elevating productivity.”
Cost Reduction and Control: The Bottom Line Advantage
In today’s fiercely competitive market, cost management is of utmost importance. Standardization paves the way for streamlined procurement and minimizes variations, thereby reducing rework expenses. Using standardized components and materials grants us better negotiating power with suppliers, translating to substantial cost savings.
According to a study by the Manufacturing Performance Institute, companies implementing strong standardization measures reported an average cost reduction of 15%.
Improved Innovation: Unlocking Creativity within Boundaries
Contrary to popular belief, standardization is an enabler of innovation, not a deterrent. By setting standardized protocols, engineers are relieved from repetitive, low-value tasks and can focus on high-impact, value-added activities.
Dr. Emily Davis, an authority in manufacturing innovation, remarks, “Standardization frees engineers from mundane tasks, allowing them to direct their creativity toward solving intricate challenges and fostering groundbreaking innovations.”
Adaptable Technology: Future-Proofing Operations
In this age of rapid technological advancement, adaptability is essential. Standardization assures that our procedures can integrate evolving technologies seamlessly. By embracing flexible standards, we effectively future-proof our operations.
Technology analyst Michael Chang points out, “Companies that incorporate standardized, modular systems are better poised to leverage the benefits of emerging technologies.”
Conclusion: Thriving in the Age of Standardization
Standardization is not just a choice but an imperative in today’s dynamic and competitive market. Structured processes, cost control, innovation enhancement, and technological adaptability are interconnected elements that provide a robust foundation for any manufacturing company.
As we continue our relentless pursuit of excellence, we are unwavering in our commitment to standardization. This commitment ensures not only operational efficiency and cost-effectiveness but also promotes a culture of innovation that sets us apart in the industry.
If you’re keen to explore how standardization can transform your manufacturing processes, or if you’d like to be notified each time we release a new blog post, please fill out our contact form for a complimentary consultation and updates.